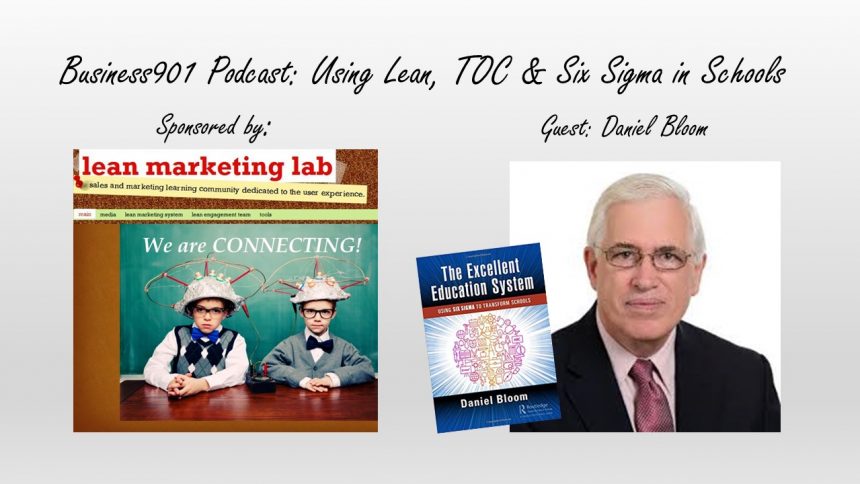
Using Lean, TOC & Six Sigma to Transform Schools
The Excellent Education System: Using Six Sigma to Transform Schools helps you discover and understand the technique of evidence-based learning and operations through which the modern school satisfies the need to increase the flow of successful students through the educational system from Kindergarten through Grade 12. This book explains, in clear terms, what educational excellence means and the Read More …